Innovative Lösungen im 3D-Druck für die Luft- und Raumfahrt
Die Kooperation mit Institutionen wie dem Deutschen Zentrum für Luft- und Raumfahrt (DLR) unterstreicht die Bedeutung der 3D-Drucktechnologie für Bauteile, die spezielle Anforderungen erfüllen müssen. Mit der Entwicklung von Prototypen, beispielsweise für die Gruppe Mess- und Sensortechnik der Einrichtung Flugexperimente, und dem Potenzial einer anschließenden seriellen Fertigung per 3D-Druck, können innovative Lösungen für die Herausforderungen in der Luft- und Raumfahrt realisiert werden. Mit der Nutzung additiver Fertigungsverfahren wie der LCM-Technologie für technische Keramiken oder dem LaserMelting-Verfahren für Metalllegierungen eröffnet CADdent als innovatives Fertigungszentrum neue Perspektiven für die Zukunft dieser Branche. Erfahren Sie in diesem Beitrag mehr über einen unserer hergestellten Sensoren und die dafür verwendeten Hochleistungsmaterialien sowie über die Kooperation mit dem DLR.
Keramik 3D-Druck für spezielle Anwendungsbereiche
Der Keramik 3D-Druck vereint die verfahrensspezifischen Vorteile der additiven Fertigung mit den werkstoffspezifischen Vorteilen von technischen Keramiken. Dadurch ergeben sich weitläufige Anwendungsbereiche bis hin zu Spezialgebieten, in denen an das jeweilige Bauteil Maximalanforderungen gestellt werden. Dies trifft beispielsweise auf die Luft- und Raumfahrttechnik zu. In dieser Branche werden je nach Bauteil und dessen Einsatz explizite Anforderungen hinsichtlich Mechanik, Aerodynamik oder Temperatur gestellt – weshalb nur wenige Materialien dafür in Frage kommen.
Vorteile von technischen Keramiken
Technische Keramiken wie beispielsweise Aluminiumoxid oder Zirkoniumdioxid besitzen eine sehr hohe Festigkeit und eine enorm gute Beständigkeit gegenüber Chemikalien, Korrosion und Temperatur. Sie sind zudem elektrisch isolierend und biokompatibel. Darüber hinaus überzeugt Aluminiumoxid mit dem Potenzial einer Gewichtseinsparung, da es sich hierbei um eine sehr leichte Keramik handelt.
Vorteile der additiven Fertigung
Durch die additive Fertigungsweise lassen sich äußerst komplexe, filigrane sowie hohle Strukturen kostengünstig und in sehr kurzer Zeit herstellen. Dabei ist die additive Fertigung sowohl für die Einzelteilefertigung, beispielsweise zum Prototypenbau, als auch für die serielle Fertigung von Klein- oder Großserien geeignet. In der Fertigung von technischen Keramiken setzt CADdent auf das LCM-Verfahren (Lithography-based Ceramic Manufacturing) des Maschinenherstellers Lithoz GmbH – dem Marktführer im Bereich des lithographie-basierten Keramik 3D-Drucks.
Dentallegierungen in der Luft- und Raumfahrt
Neben der Expertise im 3D-Druck mit technischen Keramiken verfügt CADdent über jahrelange Erfahrung in der additiven Fertigung verschiedener Metalllegierungen, wie Kobalt-Chrom und Titan. Diese beiden Hochleistungswerkstoffe werden in der Dentalindustrie eingesetzt und weisen im Vergleich zu herkömmlichen Stahllegierungen eine deutlich höhere Härte und Korrosionsbeständigkeit auf. Zudem besticht Titan – der Werkstoff der Zukunft – durch seine Leichtigkeit, die auf die vergleichsweise niedrige Dichte zurückzuführen ist. Daher besitzen beide Dentallegierungen ebenfalls ein hohes Potenzial für den Einsatz in der Luft- und Raumfahrtindustrie. Mit der additiven Herstellungsweise im LaserMelting-Verfahren können enorm dünnwandige und komplexe Geometrien hochpräzise erzeugt werden, die mit Fertigungstechniken wie zum Beispiel dem Fräsen nicht realisierbar sind.
Erfolgreiche Kooperation mit dem DLR
Seit 2023 sind wir Fertigungsdienstleister für das Deutsche Zentrum für Luft- und Raumfahrt (DLR) zur Entwicklung von Prototypen und anschließender Produktion von Kleinserien für die Gruppe Mess- und Sensortechnik der Einrichtung Flugexperimente. Eines unserer Projekte umfasste die Herstellung eines Prototypen für einen PT100 Sensor, der bei Flugexperimenten mit dem Flugzeug "HALO" (High Altitude and Long Range Research Aircraft) benötigt wurde. Dieser Temperatursensor besteht unter anderem aus Platin (Pt) und weist bei 0 °C einen Widerstand von 100 Ohm (Ω) auf. Durch intensive Zusammenarbeit mit unserer Forschungs- und Entwicklungsabteilung konnten Designanpassungen getroffen und die Topologie optimiert werden.
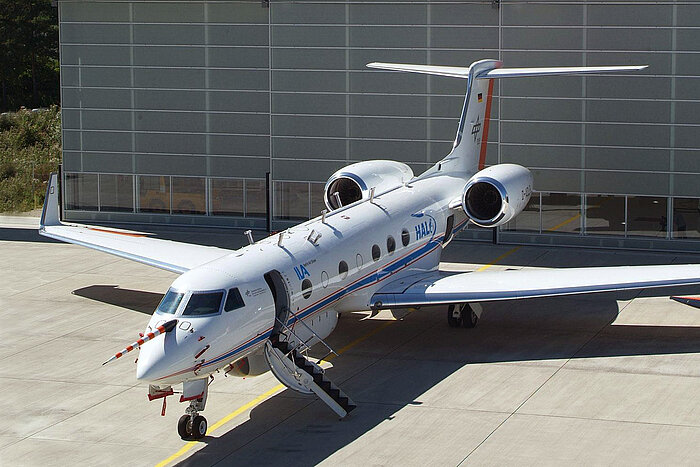
Flugzeug ADLR „HALO“, Quelle: DLR
Innovativer Temperatursensor
Das Besondere an diesem für die Luft- und Raumfahrt entwickelten PT100 Sensor ist, dass der Sensorkopf aus Zirkoniumdioxid im Keramik 3D-Druck realisiert wurde. Die additive Fertigungsweise ermöglichte es die Wandstärke des Sensors im Kopfbereich auf 0,3 mm und im restlichen Bereich auf 0,5 mm zu reduzieren. Anschließend wurde um den Kopfbereich ein 0,025 mm dünner Platindraht aufgewickelt und mit dem Kupferdraht verlötet. Der PT100 Sensor profitiert dabei von den herausragenden Werkstoffeigenschaften des Zirkoniumdioxids, wie der sehr geringen thermischen Leitfähigkeit (2,5 - 3,0 W/m*K) und der sehr hohen Temperaturbeständigkeit. Außerdem wurde der Stecker des Sensors aus Aluminiumoxid und der Anschluss aus Kobalt-Chrom per 3D-Drucktechnologie gefertigt.
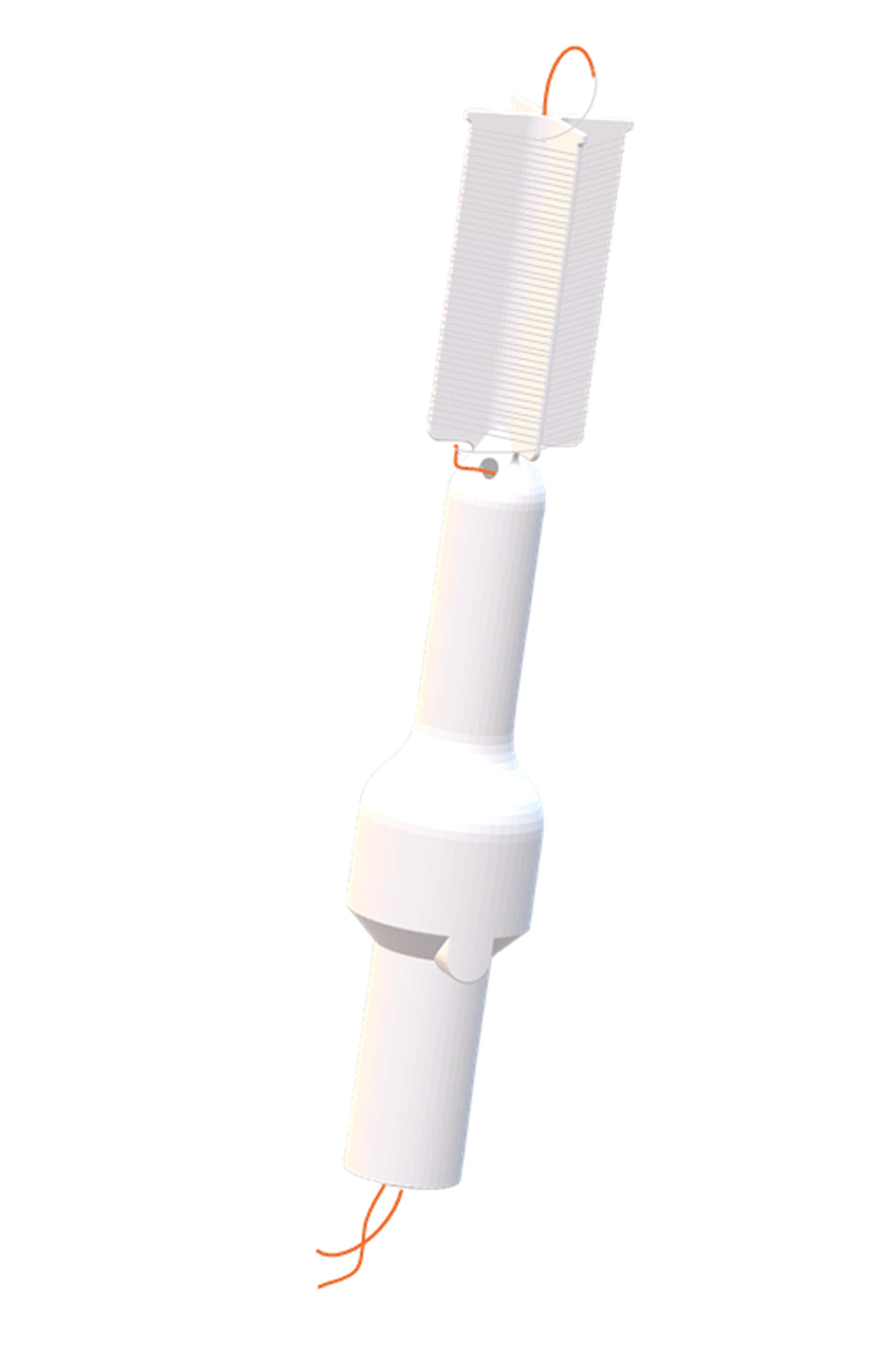
FAZIT
Die Anwendung des 3D-Drucks für spezielle Bauteile in der Luft- und Raumfahrt eröffnet neue Perspektiven für die Zukunft solcher technisch anspruchsvollen Branchen. Wenn Sie auch Interesse daran haben Prototypen oder Kleinserien bei CADdent in Auftrag zu geben, können Sie auf unserer Rapid Prototyping Bestellseite einfach und schnell den Datensatz Ihres Bauteils hochladen und im Anschluss direkt das Angebot herunterladen.
Haben Sie Fragen zu Rapid Prototyping? Unsere Expert:innen unterstützen Sie gerne bei der Auswahl des richtigen Materials sowie eventuellen Anpassungen im Design.
Prototyping Kundenservice
T: +49 821 5999965-0
E-Mail: prototyping@caddent.eu